Floor Marking
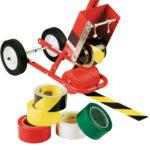
Self-adhesive floor marking tapes, specially designed for floor marking and warning marking in production and warehousing premises. This tape is widely used for marking the direction of movement of transport and workers, marking of storage areas, labeling of hazardous production areas, separation of spatial zones, marking of columns, marking of fire barriers, marking of sports grounds, etc. Tapes are an excellent alternative to other markings methots and marking with paint because it has some advantages: non-toxic, meets international environmental conditions, is not flammable, resistant to chemicals, wear-resistant, etc.
3M floor marking tapes in implementation LEAN and 5S Systems in this flyer.
Floor marking tapes are extremely convenient tool when practicing social-distancing during the Covid-19 pandemic.
When implementing 5S, think 3M.
3M’s color coding vinyl tapes can help implement the 5S system by providing floor marking and safety identification. The 3M™ Vinyl Tapes and 3M™ Safety Stripe Tapes come in a variety of bright colors that are locked into the vinyl for long term high visibility. Perfect for lane marking, hazard and safety marking of floors, loading docks, shipping areas and warehouses.
5S and Color Coding
5S was developed in Japan and was identified as one of the techniques that enabled Just in Time manufacturing. 5S workplace organization method uses a list of five Japanese words: seiri (classification), seiton (order), seisō (cleaning), seiketsu (standardization), and shitsuke (discipline).
5 steps in the 5S system:
1. Sort: Retain only the items and procedures necessary to do the job.
2. Straighten: Ensure each item is kept in a designated place.
3. Shine: Maintain clean and organized spaces.
4. Standardize: Define standards for workspaces and procedures.
5. Sustain: Keep up with established standards and procedures.
The 5S visual management system makes it easy to ensure your workplace is more organized, efficient, productive and safer. The 5S system first analyzes your workspace and removes unnecessary items. From there, it organizes essential items and efficiently cleans and maintains the workspace. Best of all, these steps quickly become part of your organization’s daily routine. Visual cues are a vital part of a successful 5S program. They help you communicate information to employees using color-coding, labeling and floor markings. Floor markings help employees recognize work cell boundaries, areas requiring special caution and locations for public spaces, such as restrooms, break rooms and recycling bins. You can get started with the 5S system today—and begin transforming your workplace.
While there are no specific floor marking color requirements, the following is a color coding guide popular in many facilities:
Pattern | Color | Examples Where to Use |
---|---|---|
|
Yellow | Aisles, walk-ways and traffic lanes, work cells |
|
Orange | Material or product inspection or temporary storage locations |
|
Red | Safety/first aid, defect/scrap area, red tag area |
|
Green | Materials and manufacturing, finished goods |
|
Blue | Materials and manufacturing, raw materials |
|
Black | Materials and manufacturing, work in progress |
|
Black/Yellow | Areas of potential health risks, extra caution needs to be taken |
|
Black/White | Areas to stay out of for operational purposes |