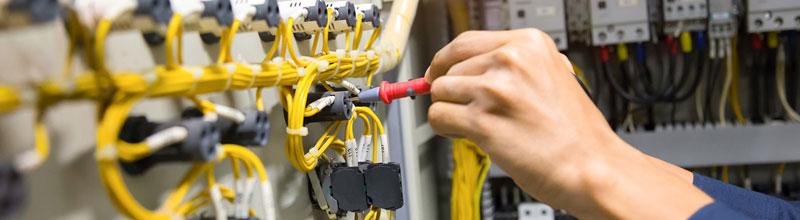
Standards and certificates are intended to ensure the safety of people and property. However, it is difficult to find detailed information on the web, since the text of the standards is protected by copyright law. Standards can be purchased from the organizations that create them. The purpose of this review is to provide general information regarding standards and certificates in the field of cable protection.
In North America the wire types and procedures are often defined by standards issued by the organizations stated below. The links below take you to the appropriate sites.
• UL
Previously known as Underwriters Laboratories, UL is an American safety certification company with offices and testing labs around the world. The U.S. Occupational Safety and Health Administration, (OSHA), trusts this organization to conduct tests to determine the performance characteristics of the products.
More…
• UL Recognized Component
This logo UL Recognized Component indicates that the product does not meet a UL standard, but is designed to be part of a UL-certified product.
More…
• ASTM
Formerly known as the American Society for Testing and Materials, ASTM is based in the United States but it is an international standards organization. There are more than 12,000 ASTM standards used worldwide in different industries from toys to cable wiring.
More…
• MIL и MS
MIL stands for military standards of the United States. They are used to improve unification and compatibility with logistics and other defense-related systems. Some of these standards have become widespread in various industries, as their compliance is necessary for the fulfillment of government contracts. The abbreviation MS stands for “military specifications”.
More…
UL
UL224 is a standard that defines the requirements for insulating tubes, which usually have a circular cross-section. They consist entirely of extruded compounds, the characteristic components of which are:
• thermosetting polymers;
• elastomers;
• thermoplastic polymers.
The requirements of this standard also cover heat shrink tubing and cross-linked tubing. In terms of applications, UL224 certified tubing is intended for use as part of the internal wiring of electrical devices and appliances. It can be used for the following purposes:
• insulation of one or more inadequately insulated conductors;
• conductive busbars;
• cables in electric motors;
• wires in transformers;
• cable lugs;
• small assemblies of electronic components.
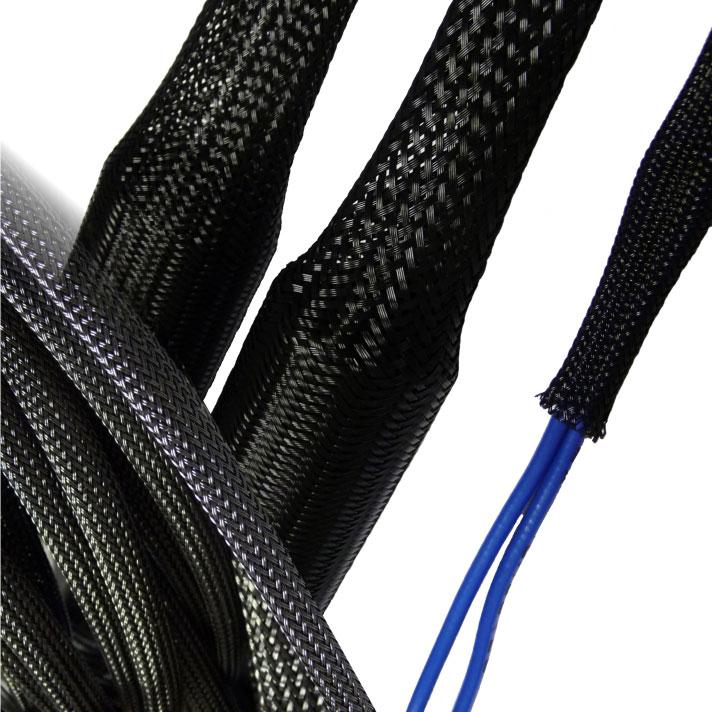
When UL224 certified tubing is used it is presumed that it will not contact with sharp edges, corners or protrusions, and it will not be stretched, compressed or repeatedly flexed. It is also not intended for use where standard insulated conductor specifically designed for such task can be used.
The following UL224 certification is often used for heat shrink tubing: 125°C VW-1 600 Volts (E204071). The VW-1 test is important. It shows that the heat shrink tubing material will not contribute to a fire by supporting combustion for an extended period of time. (Note that non-flammability of a cable protective shell is often defined as the ability to stop burning after the heat source has been removed.)
UL94 is a flammability standard for plastics. It is used, for example, to test nylon cable ducts.
Typically, UL94 certification is specified along with a flammability rating: V-0, V-1, or V-2. The testing procedure is as follows.
1. 2 sets of 10 specimens are tested for thickness each.
2. After keeping for 48 hours at 73.4˚F (23˚C) and 50% relative humidity, 5 specimens of each thickness are tested.
3. 5 specimens of each thickness are tested after 7 days at 158˚F (70˚C).
4. Each specimen is positioned so that its long axis is vertical.
5. Each specimen is clamped so that it is positioned 10 mm above a gas Bunsen burner.
6. A blue flame is then applied 20 mm high to the center of the bottom edge of the specimen for 10 seconds. If the combustion stops within 30 seconds, the laboratory staff renews the flame for another 10 seconds.
7. If the sample drips, the particles are allowed to fall from a height of 300 mm onto a layer of dry absorbent made of surgical cotton wool, which is placed below.
The results are interpreted as follows.
All classes | After each flame application, the samples cannot burn with the flame for more than 10 seconds. |
V-0 | The total burning time with flame may not exceed 50 seconds for 10 flame applications for each set of 5 samples. |
V-1 V-2 |
The total burning time with flame may not exceed 250 seconds for 10 flame applications for each set of 5 samples. |
All classes | The samples cannot burn with flame or smolder up to the holding clamp. |
Below are stated the differences between flammability classes.
V-0 | The samples cannot produce droplets of burning particles that ignite the dry absorbent made of surgical cotton wool. Nor can they sustain a smoldering combustion that lasts more than 30 seconds after the second removal of the torch flame. |
V-1 | The samples cannot produce droplets of burning particles that ignite the dry absorbent made of surgical cotton wool. Nor can they sustain a smoldering combustion that lasts more than 60 seconds after the second removal of the torch flame. |
V-2 | The samples may produce droplets of burning particles that ignite the dry absorbent made of surgical cotton wool. They may also sustain a smoldering combustion that lasts for more than 60 seconds after the second removal of the torch flame. |
UL Recognized Component
A special logo is provided for UL Recognized Components. These components are not the final product ready for installation on site, but will be installed into another device. And the UL certification logo will be placed on that final device.
For example, a cable tie may have a UL94 V-2 fire rating, but the entire product may be Recognized Component. This means that it is suitable for use inside a larger UL certified product.
ASTM
ASTM D4066 covers nylon materials suitable for injection molding and extrusion. It is approved by the U.S. Department of Defense. These materials must meet the standard’s requirements for density, tensile strength, resistance to mechanical impact, and heat resistance.
MIL and MS
MIL-M-20693 standard applies to materials, particularly molded plastic made from tough nylon, used for general purpose, weather-resistant and dielectric applications.
MS-25281 is also a military standard, but is more specific to fastening hardware, including cable ties and clamps.
Another military standard is MIL-S-23190E, which covers plastic and metal components, as well as devices for bundling and supporting cables, cable assemblies, and wires in electrical, electronic, and communications equipment.
MS-3367 contains specifications for cable ties.